Quality and technology
When, as was the case last year in Lenzerheide, a Moving Carpet retires after 20 years, in snow and ice, in wind and weather, and is replaced by a modern successor, then this is no coincidence. For it is not "only" the numerous inventions and innovations that have made the Moving Carpet the clear number 1 among Person Conveyor Belts for almost 25 years, but also the high demand for quality.
The Moving Carpet's preferred home, the mountains and glaciers of this world are a highly demanding environment that often poses great challenges to materials and technology. To develop a product that functions reliably for years and decades despite sometimes extreme temperature fluctuations, ice and snow, storms, repeated assembly and disassembly, or the stresses of up to 6,000 passengers per hour, is truly a special achievement.
Tested under extreme conditions
A conveyor belt that works in the dry and well-tempered environment of a factory hall or at a trade fair booth is one thing, but does it also work at 3,500 meters at -20° in a snowstorm? What if the weather conditions do not play along with a field test and no limit loads can be simulated? Sunkid is therefore the only manufacturer to operate its own research laboratory, where the entire product, individual components and innovations are tested under extreme conditions prior to market launch. Moving Carpet under masses of snow: Extreme climatic conditions prevail on the Jungfraujoch, 3,466 meters above sea level. The average annual temperature is -7.9 °C with fluctuations from -37 °C to +12 °C. Wind speeds can reach up to 260 km/h. Heavy icing, snowfall and avalanches must be expected at any time of year.
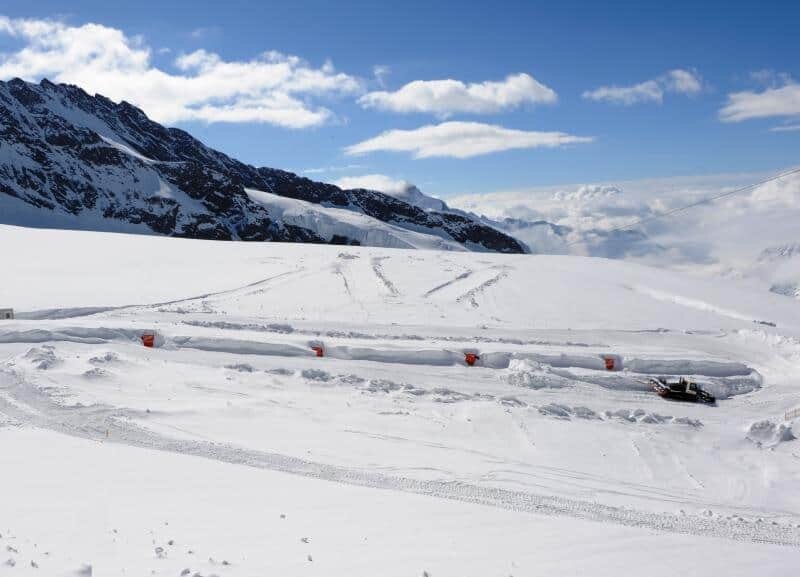
Among other things, the research center has a 30m² cooling chamber in which engineers and technicians put the Moving Carpet through its paces at up to -20°. But also specially developed and built test facilities, such as a tensioning system for determining the practical breaking force of conveyor belts and belt splices, contribute to important findings. After all, under which load, under the most varied and often changing conditions, a conveyor belt and its belt splices reach their load limit, are decisive questions. Answering these questions only on the basis of the manufacturer's specifications for the individual components was and is not an option for Sunkid. Thus, a test station developed precisely for this purpose was built by the special mechanical engineering department. In this way, not only could material tests be carried out, but the findings could also be used for new developments and improvements. Sunkid's research and development department is also located in the newly opened administration building and surrounding factory halls in 2019, at the main plant in Bruckschlögl - Bad Goisern.
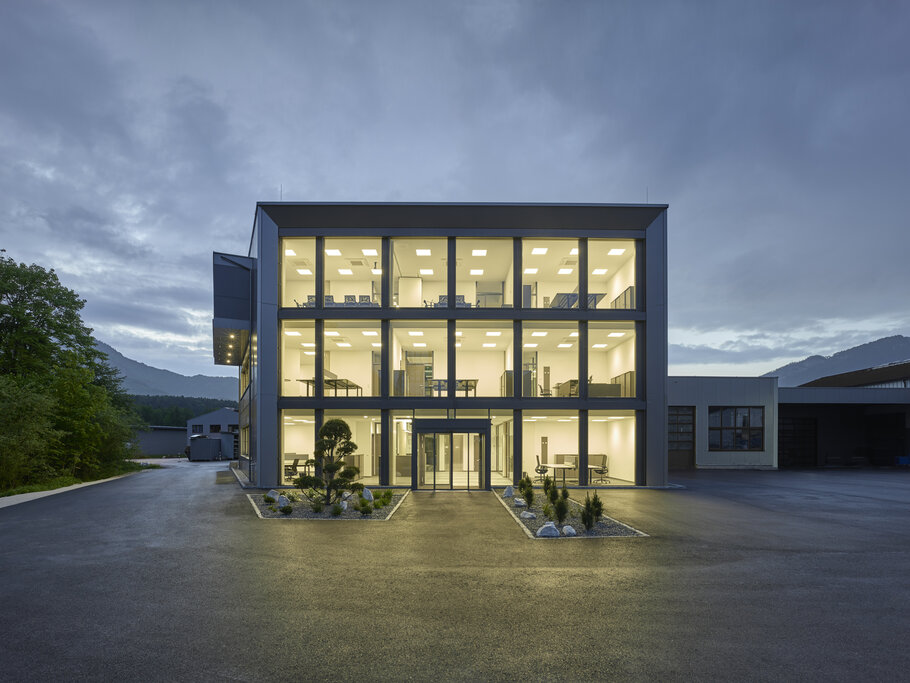
Research & development at the highest level
However, there are also subject areas and issues that cannot be dealt with directly in the R&D department and for which external specialists are indispensable. One example of this is the tests carried out in France in 2019 for high-speed conveyor belts (up to 1.2 m/s). The prestigious French Institute of Sciences and Technologies for Transport, Planning and Networks IFSTTAR, and Claude Bernard University accompanied Sunkid in the biomechanical analysis on the impact of different settings of the safety flap release resistance on the risk of injury in high-speed conveyor belts.
The objective of the study was to address the unintended release of the safety flap at high speeds and the associated emergency shutdown of the conveyor belts. This is because the unexpected stopping of the system not only affects smooth operation, but is also unpleasant for the users. However, as there have only been studies for the speed range of up to 0.7m/s from the official side so far, Sunkid invested in the elaborate investigation to make the Moving Carpet even better.
![[Translate to EN:] Mitarbeiter des IFSTTAR, und Wissenschaftler der Claude Bernard University zusammen mit Ingenieuren und Technikern von Sunkid bei der Arbeit.](/fileadmin/_processed_/9/2/csm_WP_20150512_011-1_ba19cd04d2.jpg)
The study was conducted with a crash test dummy simulating a 6-year-old child. The dummy used was a P6 child dummy, as is also used in crash tests in the automotive sector. In a whole series of test runs, the effects of the factors speed and release resistance, in changing setting variants, on a possible risk of injury were now investigated. The results of the measurements were then analyzed and categorized using the internationally recognized "Abbreviated Injury Scale". The resulting findings could now be compared with those of the STRTMG (French ropeway authority) and led to the following conclusion: "The biomechanical analysis of the head and neck injury criteria for the tests on a Sunkid conveyor belt at different speeds (0.7 and 1.2 m/s) for different drop opening configurations did not show any excess risk compared to the general study on conveyor belts previously carried out for the STRMTG." The experience and detailed values gained from this study are now being incorporated into the development of the latest generation of Moving Carpet. Whereby the designers and engineers at Sunkid will of course test the measures derived from this to the last detail again at the research center before implementation.